Fuel Reformer, Engine, and Generator System
Upon receiving a partially completed synthesis rig system from Biomass Energy Company (BEC) in 2008, Prof. Depcik has overseen the completion of this experimental setup. The rig consists of a full scale reformer, Chevy 350 small block engine, Mecc Alte ECO32-2L/4 generator, and extensive data acquisition equipment. This unique rig utilizes waste glycerin (with added water) from biodiesel production in order to produce electricity through combustion of a hydrogen rich synthesis gas (syngas) in the engine/generator setup. The rig allows for three different combustion pathways: pure propane, reformed propane, and reformed glycerin. Pure propane is used in order to determine the needed fuel flow requirements in order to run the engine and generator system. Reformed propane is utilized in order to calibrate the model of the fuel reformer including ambient heat transfer. Reformed glycerin provides the final pathway as it is broken down into a hydrogen-rich syngas through partial oxidation and steam reforming in an oxygen deficient environment over a nickel/alumina catalyst (of note, this process is highly exothermic and self-sustaining). Data acquisition is completed using a custom LabVIEW program written in-house by graduate students that records flow rates, engine performance, temperatures, and pressures along with in-cylinder pressure and crank angle measurements. Future upgrades to the rig will include increasing the size of the reformer to allow for better syngas production, upgrading the generator for additional loading capabilities, and investigation into heat recovery for biodiesel production (e.g., used in the glycerin demethylation process). Moreover, the setup can be relatively easily modified in order to utilize different gaseous fuels (e.g., natural gas or biogas) directly for power, reforming, or catalytic upgrading studies.
Research Scientist Derek Pickett is featured as part of an article about the next generation of biodiesel co-product research in Biodiesel Magazine.
Representative paper: Use of Glycerin By-product from Biodiesel Production for Power Generation
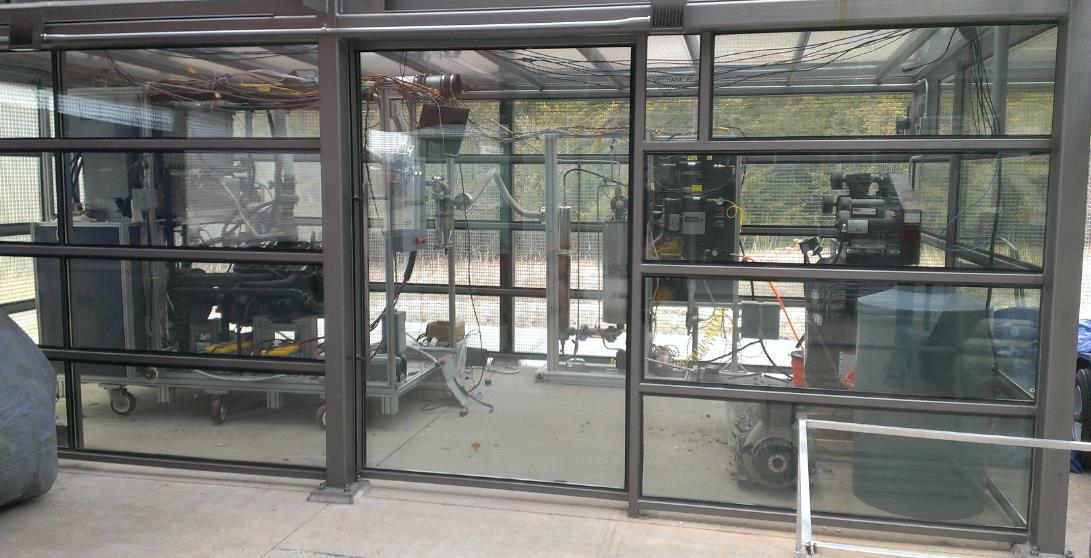



Engine | Chevy 350 V8 small block naturally aspirated spark ignition engine, four valve, 4 inch bore, 3.48 inch stroke, compression ratio 8.2:1. | |
---|---|---|
Reformer | Custom reformer with propane line, compressed air line, glycerin injection nozzle and 9000V spark plug igniter. Filled with Ni/Al2O3 catalyst. | |
Generator |
| |
In-Cylinder Pressure Analysis | Kistler 6052C piezoelectric transducer calibrated to measure from 0 to 50 bar with less than 0.5% error at up to 160 kHz, sensitivity to thermal shock less than 0.5 bar, Kistler 5011B charge amplifier with low pass filter, Kistler 2614B optical encoder and Kistler 2614B4 pulse multiplier provides 0.1 to 6 degree resolution. Devices coupled to an NI SCB-68 shielded input/output connector block. | |
Heat Exchanger |
| |
General Measurements | Equipped with sensors to monitor reformer air flow, propane flow, glycerin flow, reformer pressure, reformer temperature, generator output, relative humidity, ambient air temperature and pressure, engine intake pressure and temperature and engine intake airflow via Merriam LFE. | |
Data Acquisition | National Instruments (NI) compact-reconfigurable Input/Output (cRIO) device (model cRIO-9073) operating in conjuncture with a LabVIEW program coded in-house. |